04DIVERSIFICATION WITH SUSTAINABILITY
ENVIRONMENTAL DIMENSION
Mitigation of environmental impacts
For the Eternit Group, the environment where its companies operate is treated as an extension of their operations, seeing that protection and respect for the environment is essential for the sustainability of the business. Employees, therefore, are directed to follow the Company's environmental policies, as set out in the Program for Management Excellence (PEG in Portuguese), which are applicable to all the Company's installations.
For its initiatives in this direction, Eternit, Precon Goiás and SAMA have been granted ISO 14,001 certification (environmental management system), which attests to the mitigation of significant environmental impacts on biodiversity, such as atmospheric emissions, the treatment of effluents, and the correct disposal of residues. SAMA, furthermore, was the first chrysotile ore mining company in the world to receive this certificate. All these units follow the Environmental Management System, which is supported by a tool which is able to carry out the assessment, evaluation and control of environmental aspects of applicable to the Group's activities through the cross-referencing of information on Federal, State and Municipal legislation. This tool is based on FMEA (Failure Mode and Effect Analysis) methodology. All applicable legal requirements are controlled in such a way as to guarantee the full compliance of each and every one. EN26
Tégula, recently acquired by Eternit, is still undergoing the ISO 14,001 certification process. For this reason, the company is implementing processes for the control of air, land and water pollution. An example of this is the adoption of synthetic mould releasing agents, instead of diesel oil, for the releasing of tiles from their moulds, among other initiatives. EN26
The subchapters that follow go into further detail about the initiatives of the Eternit Group with respect to the mitigation of environmental impacts, referring to the type of impact and natural resource affected.
In 2010, investments in the disposal of residues, treatment of emissions, mitigation of impact, prevention actions and environmental management jumped from R$ 3.9 million, to R$ 6.7 million, due to the higher costs of the dust removal systems, and increased depreciation as result of the installation of the new fibre production lines, in addition to the replacement of filter ducts at the mining company SAMA. EN30
Type of cost | Cost breakdown | 2010 | 2010 Pro-forma(*) | 2009 | ||||
Cost of the disposal of residue, the treatment of emissions and expenses to mitigate the following items: | Treatment and disposal of residues | 1,143 | 1,142 | 518 | ||||
Treatment of admissions | 1,643 | 1,643 | 525 | |||||
Certificates of emission | 54 | 54 | 53 | |||||
Depreciation, materials and maintenance | 493 | 493 | 260 | |||||
Insurance for environmental responsibility | - | |||||||
Cost of total cleaning | 1,409 | 1,409 | 141 | |||||
Total | 4,742 | 4,741 | 1,496 | |||||
Costs of prevention and environmental management based on expenses related to the following items: | Education and training | 170 | 169 | 26 | ||||
External environmental management services | 513 | 504 | 126 | |||||
External certification | 116 | 116 | - | |||||
General environmental management activities | 16 | 14 | 8 | |||||
Research and Development | 5 | 5 | - | |||||
Expenses of installing clean technology | 35 | 35 | 15 | |||||
Other costs of environmental management | 1,148 | 1,148 | 2,318 | |||||
Total | 2,002 | 1,991 | 2,492 | |||||
Total | 6,744 | 6,733 | 3,989 |
(*) For comparison purposes the figures from subsidiary Tégula have not been included.
As a result of investment in initiatives to mitigate environmental impacts, in 2010 no company in the Eternit Group received any significant fines, or was subject to non-monetary sanctions, due to non-compliance with environmental laws and regulations. EN28
MATERIALS
Eternit employs a zero reject policy, in other words, 100% consumption of materials, including packaging. At the fibre cement production units, breakages are re-crushed and used again in the mixture, there being no industrial residue generated by the production process. Products that do not comply with quality standards are also reused in the process, while even office writing paper is recycled in the manufacture of tiles. Furthermore, water does not leave the installations of the plant, being maintained in a closed circuit, thus retained and reused in the manufacturing operation. While water used in the administration area is also treated and reused for the irrigation of the gardens. Some units also employ rainwater catchment.
Exceptions to this are: oily sludge, felt, hoses, tyres and metals scrap, which are sent to specialist companies for disposal. Other materials are recycled under the RECICLAnit program, which since 2006 has maintained containers at the plants for the receiving of recyclable material, which is subsequently sent to recycling co-operatives and companies. At SAMA, this project falls under the responsibility of the Sambaíba project, in alignment with the 3Rs concept – Reduce, Reuse and Recycle.
Compared to 2009, the increased in the consumption of materials is due to the expansion in the production of chrysotile ore, fibre cement products, new products that use more paint and tint, and the incorporation of Tégula.
The table below shows the ratio of materials used in the Company's production process, as well as the percentage of inputs recycled: EN1 EN2
Materials used by weight and volume/percentage recycled - Consolidated | Raw Material | Input | Quantity 2010 | Quantity 2009 | Unit | Direct | Non-renewable | Recycled | ||||||||||
Fibre cement roofing and construction systems | Chrysotile ore | X | 68,465.56 | 51,883.65 | t | X | X | |||||||||||
Lime | X | 146,345.38 | 121,012.09 | t | X | X | ||||||||||||
Recycled pile (newspapers) | X | 11,781.47 | 10,180.89 | t | X | X | ||||||||||||
Cement | X | 446,020.58 | 361,923.14 | t | X | X | ||||||||||||
Steel coils | X | 619.39 | 138.70 | t | X | X | ||||||||||||
Filler | X | 17,989.70 | 22,035.34 | t | X | |||||||||||||
Lime residue (Lama Call) | X | 4,594.24 | 2,239.35 | t | X | X | ||||||||||||
Polyethylene resin | X | 1,507.71 | 459.36 | t | X | X | ||||||||||||
Aluminium paint | X | 9,702.00 | 3,929.00 | L | X | X | ||||||||||||
Ceramic paint | X | 216,904.42 | 1,861.11 | L | X | X | ||||||||||||
Wood offcuts | X | 9,527.70 | 10,181.72 | t | X | X | ||||||||||||
Pine sheets | X | 2,411.90 | 2,091.67 | t | X | X | ||||||||||||
Wood (Pallettes) | X | 119,771.28 | 85,594.65 | m³ | X | X | ||||||||||||
Other liquid materials | X | 1,174,105.42 | 444,803.92 | L | X | |||||||||||||
Others | X | 3,086.90 | 1,820.82 | t | X | |||||||||||||
Concrete roofing and accessories | Cement | X | 45,505.29 | - | t | X | X | |||||||||||
Sand | X | 203,354.83 | - | t | X | X | ||||||||||||
Filler | X | 1,793.17 | - | t | X | X | ||||||||||||
Pigment | X | 368.47 | - | t | X | X | ||||||||||||
Varnish | X | 210.86 | - | t | X | X | ||||||||||||
Soya leticine | X | 36.42 | - | t | X | |||||||||||||
Pine lath | X | 112.94 | - | t | X | |||||||||||||
Pine material | X | 184.22 | - | t | X | |||||||||||||
Stretch film | X | 37.98 | - | t | X | |||||||||||||
Other liquid materials | X | 700,489.77 | - | L | X | |||||||||||||
Chrysotile ore mining | Ore | X | 4,870,538.69 | 4,708,303.09 | t | X | X | |||||||||||
Sterile rock | X | 11,328,058.00 | 8,580,976.00 | t | X | X | ||||||||||||
Plastic | X | 269.97 | 254.92 | t | X | X | ||||||||||||
Wood (Pallettes) | X | 4,154.22 | 4,036.28 | t | X | |||||||||||||
Various | X | 17,134.64 | 14,836.85 | t | X | |||||||||||||
Packaging bags | X | 5,755.50 | 573.07 | t | X | X | ||||||||||||
Total inputs used by the Eternit Group | 17,210,087.26 | 13,892,946.94 | t | |||||||||||||||
Total inputs used by the Eternit Group | 2,101,201.61 | 450,594.03 | L | |||||||||||||||
Total inputs used by the Eternit Group | 119,771.28 | 85,594.65 | m³ | |||||||||||||||
Total non-renewable materials | 17,137,975.26 | 13,843,593.05 | t | |||||||||||||||
Total non-renewable materials | 2,101,201.61 | 450,594.03 | L | |||||||||||||||
Total direct materials | 17,147,391.70 | 13,850,217.65 | t | |||||||||||||||
Total direct materials | 226,606.42 | 5,790.11 | L | |||||||||||||||
Total direct materials | 119,771.28 | 85,594.65 | m³ | |||||||||||||||
Percentage recycled | 0.31% | 0.36% | t | |||||||||||||||
Percentage recycled | 100.00% | 100.00% | m³ |
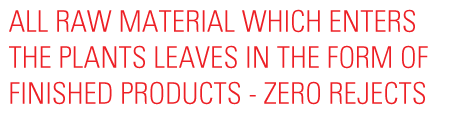
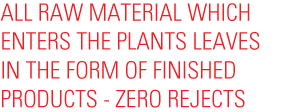
The residues from the production process are sent to specialist companies for correct disposal. Eternit Group companies do not import or export residues, only dispatching its dangerous residues for proper treatment, not having any significant spillages. EN22 EN24
With regard to spillages, none of the three companies Eternit, Precon Goiás or Tégula recorded any significant occurrences in 2010. While at SAMA, spillage of occurred of approximately 400 litres of oil due to the rupture of an internal part of the crusher, and 200 litres of oil from the tank of one of the extraction machines. The locations where the spillages took place were covered with sawdust to absorb the residue, which was subsequently collected and sent for co-processing. Once the sawdust had been removed, these locations were washed down with a special product, with the effluents generated being sent to an oil and water separation tank. There was also the spillage of 20 litres of degreasing agent during the transfer of containers in the warehouse, which was pumped to another container and reused in the heavy machinery area. None of the spillages affected either water bodies or soil. EN23
To maintain continuous improvement, Eternit constantly establishes targets and programs to reduce impacts on the environment. In addition to this, the mining company deposits tailings and sterile rock from the extraction process in banks – areas which, when no longer added to, are recovered for planting with a variety of plant species from the Brazilian cerrado. In 44 years of activity, more than 1,037,000 m² have been re-covered with vegetation.
PACKAGING
Eternit and Precon Goiás re-use 100% of the chrysotile ore packaging in the fibre cement manufacturing process. Additionally, all the finished products shipped out by these units use wooden planks and offcuts from sawmills
in their packaging, which can also be recovered. In 2010 the reuse of these materials resulted in a saving of approximately R$ 331,000. For the raw materials – cement and lime – no packaging is required because they are stored in silos. EN27
In 2010, 800 pallets were returned to the mining company from the plant at Goiânia to be re-formed and reused in the packaging of the end-product, being sufficient to package 1,600 tons of finished product. At SAMA, the production left over after the formation of complete pallets, was formed into new lots. These leftovers resulted in the use of 1314 tons of chrysotile ore, equivalent to the saving of 26,280 raffia bags. The pallets themselves are made from wood offcuts, there being no suppression of vegetation for the production of these items, in compliance with SAMA's environmental preservation policies.
ENERGY
Eternit purchases electricity from the distributors in states where its production units are based. The Company's goal is to reduce electricity consumption, and to this end, a demand control system has been installed, whose function is to free up power at peak periods, when consumption is at its highest. The total consumption of indirect electric power bought from the distributors in 2010, amounted to 126.4 million KWh (in 2009 the figure was 114.0 million KWh), with 56% of this consumption corresponding to the mining company, 2% to Tégula and the remainder to Eternit. EN4 EN5
In order to save electricity, SAMA uses a power management system similar to that used by Eternit, in addition to initiatives carried out under the 6 Sigma program, resulted in a reduction of 0.8% in consumption in 2010, compared to 2009 (respectively 236 Kwh/ ton de of fibre produced and 238 Kwh/ton of fibre). The plants in the Group have also been adopting solutions in this regard. The plant at Colombo, for example, has a wood-fired boiler that generates electricity which is heated from packaging and the wood offcuts resulting from the wall panel production process. This same plant, in 2010, installed its own generation system, which is used at peak hours. This system resulted in a saving of R$ 631,000. At the plant at Simões Filho (BA), which installed its own generation plant in June, 2010, the saving amounted to R$ 195,000 up to December.
Another economy measure, which included all the production plants, was the control of surplus reactive agents,
resulting in the saving of R$ 33,000. Tégula has also adopted measures to minimise consumption. At the affiliate in Frederico Westphalen (RS), refurbishment was carried out of the thermal insulation of the hot water ducts and the entire hot water flow system was insulated with fibreglass wool, from the heat generation point to the consumption areas (curing chambers). The pump valves, the heat exchangers and the air ventilators were also re-covered. While at the plant at Içara (SC), presence sensors were installed on the light switches in the dressing rooms, in the accessory warehouses and in the boiler room (equipment for the generation of hot water).
At the unit at Atibaia (SP), one of the largest solar panel systems in Latin America was installed, using more than 600 panels. This major investment had the aim of replacing the fossil fuel used in the heating of the curing chambers, with the use of solar powered heating in the production process. In this way Tégula has been demonstrating its concern about the rational use of inputs, as well as the well-being of its employees, and the region where operates.
There is also a project to install generators in all the fibre cement plants by the end of 2011, to generate electricity at peak hours using biodiesel. This works on an arrangement whereby Petrobras is paid in accordance with the biodiesel used, while the system can also be used for emergency power generation. EN5 EN6
The Company's energy matrix also includes sources of alternative energy, as shown in the table below: EN3
DIRECT ENERGY CONSUMPTION, LISTED BY POWER SOURCE
Consumption of Direct Energy | Unit | 2010 | 2010 Proforma (*) | 2009 | ||||
Natural Gas | m³ | 3,291,379.00 | 3,291,379.00 | 114,358.00 | ||||
LPG | m³ | 325,412.52 | 187,986.75 | 846,049.76 | ||||
Diesel Oil | L | 799,088.49 | 569,528.00 | 3,740.00 | ||||
Biodiesel | L | 8,925,397.00 | 8,614,969.00 | 6,945,838.52 | ||||
2A oil | L/Kg | 2,119,458.00 | 2,119,458.00 | 4,691,513.59 | ||||
Charcoal | m³ | 49,580.14 | 515.14 | - | ||||
Acetylene | kg | 1,925.30 | 1,613.00 | 5,902.00 | ||||
Oxygen | m³ | 4,491.21 | 4,246.21 | 18,167.70 | ||||
Vegetable Oil | ton | 2.43 | - | - | ||||
Ethanol | L | 894.00 | 894.00 | 624.00 |
* For comparison purposes, the figures from subsidiary Tégula have not been considered.
In 2010, the group significantly increased its consumption of natural gas compared to 2009, with consumption increasing from 114,358 m3 to 3,291,379 m3 – as a result of increased production capacity and the replacement of fossil fuel (2A oil) in the chrysotile ore drying furnaces with natural gas and LPG (liquefied petroleum gas), which is less polluting, emits little CO2, does not emit SOx and does not emit particles into the atmosphere, thus avoiding contamination of the soil or water tables. With this, SAMA has reduced the consumption of 2A oil which is more polluting than natural gas and LPG. At Tégula, at its plant at Içara (SC), the Capacitor Bank was increased, resulting in an accumulated reduction of 86,902 kQh from August to December 2010. EN6 EN7
EMISSIONS
The plants of Eternit Precon Goiás and the mining company SAMA assessed their direct greenhouse gas emissions for the first time in 2010. To this end, the Group used the methodology of GHG Protocol Brasil, the national program for the accounting, quantification and publicising of corporate greenhouse gas emission inventories. The plants emitted 8,979.18 equivalent tons of CO2 in the year, while SAMA emitted 6,875.50 equivalent tons. EN12 EN16
At the plants, the inventory was adopted in 2010 as a measure to quantify possible impact on biodiversity, carrying out mapping of emissions and verify possible areas for technological improvement and reduction in emissions, with a view to complying completely with the requirements of ISO 14,001 certification. The measurements carried out this year did not include indirect mobile combustion. While the indirect emissions as a result of electricity generation were accounted for under Scope 2, amounting to a total volume of 2,004.34 equivalent tons. According to GHG, Scope 2 includes emissions which are a consequence of the Company's activities, but which take place at sources which do not belong to, or are not controlled by its. While Scope 1 covers direct emissions, in other words generated by activities which belong to, or which are controlled by the Company. EN18 EN17 EN29
SAMA also began measuring its greenhouse gas emissions in 2010. The mining company currently measures the index of black smoke emitted by all diesel-powered vehicles that operate at the industrial plant and those which enter the company for the transport of products and the unloading of materials and inputs. It also measures the black smoke emitted by 72 pieces of diesel-powered equipment, 45 or which are used for the transport of rock, 15 for the unloading of rock and 12 with a support function, as well as its fleet of light vehicles powered by biodiesel – 52 in all. The results of these measurements are within or below Standard 2 on the Ringelmann scale, which is a graphic scale used for the colorimetric measurement of smoke density, this being the maximum amount permitted by law. Those vehicles which do not conform to this smoke emission requirement are prohibited from entering the Company's stockyard, until they have been rectified. Furthermore, SAMA has carried out tests with LPG and natural gas in the ore drying process, and although the results are still not yet conclusive, a significant environmental gain has been achieved, as this is a clean form of energy, which does not produce toxic residues, and has low emissions of carbon monoxide, nitrous oxides and sulphur oxides. This source of energy is included in the Kyoto Protocol. EN17 EN29 EN18
At all the plants, as well as the mining company, assessments and data collection are carried out as part of the mapping process, in accordance with the Management System, so as to facilitate integration with existing data, as well as standardising the nomenclature and methods of assessment, and taking advantage of the already established definition of responsibilities. EN16
Tégula does not yet account for a report on its emissions, but it is starting the monitoring of water heating equipment, powered by LPG. In March 2011, it began to measure the black smoke emitted by a sample of trucks that transport its products, using Ringelmann methodology. While all the diesel-powered vehicles owned by Tégula will also be analysed. These initiatives are part of the efforts being made to achieve ISO 14,001 certification. EN16 EN17 EN29 EN20
With regard to the ozone layer, none of the units of Eternit or Precon use noxious substances which are covered by Annexes A, B, C and E of the Montreal Protocol. Neither SAMA nor Tégula use substances of this type. In the latter, for example, refrigeration equipment uses R22 gas, which is not harmful to the ozone layer. EN19
With respect to particle emissions, the plants control air quality on a half-yearly basis, with measurements being taken at various points of the quantity of fibres/cm³ in the air. The limit established by the National Agreement for the Use of Chrysotile Ore is 2.0 fibres/cm³ of air, but the practice of the Eternit Group is to keep this level to under 0.1 fibre/ cm³. Monitoring is also carried out at all the exit points of the dust removal systems and chimneys, in accordance with resolution 054/06 – of the Environmental Secretariat (SEMA). EN20
SAMA has the largest system of filter ducts in Latin America, consisting of more than 17,000 filter elements. Environmental and occupational measurements are always below the mining company’s target of 0.1 fibre/ cm³). The environmental measurements taken, which follow international standards that fall outside the scope of Federal Law, registered indexes that are similar to those of any town or locality, seeing that this fibre occurs naturally and exists in air and water throughout the planet.
WATER
Despite the increase in production capacity, the water consumption of the Eternit Group in 2010 was 2.38% less than 2009 as a consequence of reduction measures adopted. At the plants of Eternit and Precon Goiás, all the water used in the production process is stored in decantation tanks for subsequent reuse in the production process, with the only loss taking place as a result of evaporation. All these units use a closed circuit in which the water in the production process is entirely reused in production, with none of this water being run off. The units also use sewage treatment stations, which are responsible for the capturing, treatment and disposal of sewage effluent generated by the use of water from the Company's human consumption. After treatment, the water is reused for the irrigation of green areas. The Company as yet does not measure the amount that is discarded, but guarantees that this discharge does not significantly affect related water bodies or habitats; nor are there any discharges in any humid zones included on the list of the Ramsar Convention. EN8 EN10 EN21 EN25
In 2010 SAMA consumed 1,527,000 m³ of water from three distinct sources. Surface water is from the Bonito River, 669,000 m³ was pumped and treated at the ETA?, while 74,000 m³ was captured in-natura by water tanker trucks during the drought period. These amounts, 47.11% less than the limit of 50 litres per second, are described in the reports on ETA Extraction/Mining (Centralised Room – Industrial Systems). The water is stored at the bottom of the caves derives from rainwater and the lowering of the water table, in the proportion of 40% and 60%, respectively, and is used in the industrial process for the dampening of tracks and tailings; the volume of the sources is estimated and the calculations to determine their origins refer to the size of the area of influence in relation to rainfall and the area surrounding the caves, taking the rainfall rate in 2010. The Bonito River has a recorded flow rate of 1,576,800 m³/ (50 litres/second x 60 x 60 x 24 x 365 = 1,576,800,000 litres/second).
From June, SAMA reused 15,000 m³ of recycled/recirculated water, pumped from the decantation tank located beyond the maintenance workshop and the stabilisation lake of the sewage treatment centre, for the process of dampening the industrial tailings from the processing operations. This figure represents 1.12% of the total volume of water used by the Company.
Part of the water in the caves, which must be emptied in order to continue the mining process, is sent to the turtle and alligator lakes (decantation lakes) and subsequently returned to water bodies (Caju Lake and Amianto Creek) or used for the dampening of tracks, industrial tailings and rock faces to be broken up. In this latter case, the water either runs off or is evaporated, and cannot therefore be reused. The industrial effluents resulting from processing and the washing of impermeable tracks are sent to the decantation tanks, and subsequently to stabilisation lake. At the effluent treatment stations, the difference in volume treated (146,245 m³) and discarded (94,670 m³) is due to the quantity of sediment carried in the crude effluent, whose separation is carried out through a filtration process, combined with the evaporation that occurs during the drying process on the beds prepared for this purpose, in addition to the water run-off which goes to the stabilisation lake. Samples are taken periodically to measure and monitor the quality of effluent discharged into the Amianto Creek (some on a daily basis, others half-yearly), whose standards must comply with the limits established by Conama resolution 357/2005. The results of the analyses and assessments made by employees of the companies Ecomaj and Conágua Ambiental attest to the Group's compliance with the legislation.
After the biological treatment at the Effluent Treatment Station, the run-off is sent to the stabilisation lake, before being discharged into the Amianto Creek, whose average flow in 2010 was 54.0 litres/second (Conágua and Bioagri/2010). In this water body periodical chemical analyses are carried out for the evaluation of effluent quality (some on a daily basis, others half-yearly), in compliance with the standards established by Conama Resolution 357/2005. The results of the analyses and assessments made by employees of the companies Ecomaj and Conágua Ambiental attest to the Group's compliance with the legislation. With regard to the total flow volumes (1,702,944.0 m³/year) and discharge (94,670 m³/year), 0.06% of effluent was discharged into the Amianto Creek. EN8 EN10 EN21 EN25
Tégula also makes efforts to reuse water, again collecting part of the volume generated in the cleaning of the varnish application machines. Currently 60% of the water is reused, but the company is making efforts to improve its system of reuse, which also has an open concrete tank which, on rainy days, overflows into a pluvial gallery. EN10
Lastly, in 2010 no water source was significantly affected by the withdrawal of water for the carrying out of the Eternit Group's activities, taking into account the criteria of volume withdrawn, sensitivity of the ecosystem and the established protection area. In addition to this, there was no need to carry out any drainage for the realisation of any of the Group’s activities. EN9
Total water withdrawn by source | 2010 | 2010 Proforma (*) | 2009 | |||||
Surface water | Humid areas | |||||||
Rivers | 742,714.74 | 742,714.74 | 957,545.28 | |||||
Lakes | ||||||||
Oceans | ||||||||
Subterranean water | ||||||||
276,037.03 | 262,268.43 | 392,872.11 | ||||||
Rainwater | Collected / Stored | 621,864.00 | 621,864.00 | 450,000.00 | ||||
Effluents from other organisation | ||||||||
Municipal supply | 141,234.47 | 133,769.47 | 25,050.40 | |||||
Supply (others) | ||||||||
Total m³ | 1,781,850.24 | 1,760,616.64 | 1,825,467.79 |
(*) For comparison purposes the figures from subsidiary Tégula have not been included.
PLAN FOR THE REVITALISATION OF DEGRADED AREAS
In the mining of chrysotile ore the soil removal is restricted only to the locations where extraction is to be carried out at the rockface, the depositing of sterile rock from the mine, and the tailings from the industrial processes, all aspects which are carried out with the authorisation of the environmental body responsible. The soil removal is carried out by an excavator and the soil removed is transported in dump trucks to the deposit piles. Part of the removed soil is used directly for the revitalisation of the tips of sterile rock and tailings (when they will no longer be added to) while part is stored separately for later use. The main objectives of re-vegetation is to reduce the visual impact of the deposits of sterile rock and tailings as well as protecting these tips from water and wind erosion. The revitalised areas are inspected periodically to check the growth of the protective vegetation on the soil. If necessary, SAMA carries out corrective measures went imperfections are detected.
Areas impacted by mining activity in Brazil have their revitalisation guaranteed through PRAD (Plan for the Revitalisation of Degraded Areas). At SAMA, the plan is implemented after extensive planning of the mining activities envisaged for the future.
The caves of the mining company, despite being deep (currently approximately 170 meters in depth), follow angles that are geo-technically stable in terms of their banks, defined as a result of studies carried out by the IPT (Institute for Technological Research and Higher National Mining School) in Paris.
At the end of the activities, forecast to be in 31 years time, the caves will be used to form lakes which will be filled with subterranean water and rainwater, offering a variety of possible uses, such as the breeding of fish for fishing sport, recreation, watersports and others. Beside the caves, a camping area is planned, with car parking, bathrooms, administration, access for boats, a playground and other leisure structures.
The banks of sterile rock and tailings will be stabilised geo-technically and totally re-covered with soil and vegetation. The parts that cannot be re-covered while the mine is still in use, will be covered once the activities come to an end. On one of the tips, a panoramic view point is planned, with a plaque explaining the various observation points, with a car parking area, and landscaping.
A portion of the buildings, such as the bathroom, canteens, workshops and others, can be used for other purposes, such as:
- A museum on the history of chrysotile ore, with photographs, mineral samples and equipment used during the mine extraction phase;
- Headquarters for the administration of the leisure area;
- Water and sewage treatment stations, developed to serve the housing estate and the remaining buildings, and
- After the end to activities at SAMA, part of buildings could be used for the creation of an industrial area in the municipality.
The provisional schedule for the implementation of PRAD following the closure of the mine has been drawn up for the period 2042 to 2051. The document includes the various stages of mine deactivation and cleaning, the management of infrastructure, stabilisation and preparation of the soil, engineering works and monitoring. The investment budget for the revitalisation of the site after the mine's closure is approximately R$ 10 million. Following the end of mining activities, monitoring of the revitalised area will continue until it has completely stabilised. SO1 EN14
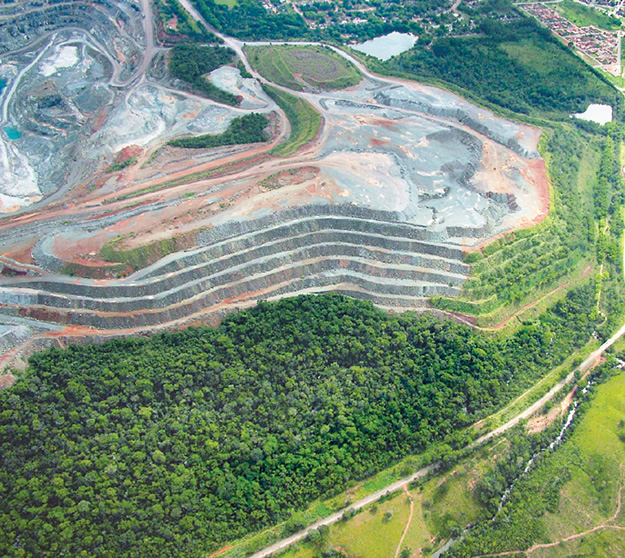
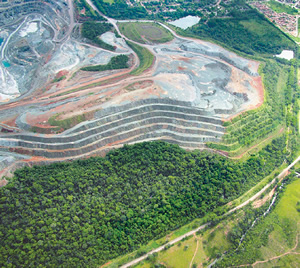
Revegetation of the banks of tailings from the mining company SAMA
BIODIVERSITY
None of the activities of the Eternit Group affects species present on the red list of the IUCN (International Union for Conservation of Nature). Furthermore, the Group preserves and maintains environmental reserves at its manufacturing plants at Colombo (PR), Simões Filho (BA) and Atibaia (SP), as well as SAMA. The plant at Colombo occupies 58,377 m² of the Environmental Preservation Area (APA in Portuguese – conservation units set up by the public authorities) of Iraí, which extends for 115 Km², over an area covering five municipalities. Encroaching on part of the Serra do Mar, this APA has flat regions which are a transition area between mixed sub-tropical moist forest, also known as the Forest of Araucária, and dense subtropical moist forest, covering one of the last remaining water meadows. The plant also maintains a partnership with the NGO SPVS – Society for wildlife research, with a view to providing environmental education to revitalise its reserve and riverbank vegetation.
The plant at Simões Filho is located in the APA – Joanes/Ipitanga, in the region of the lower hydrographic basin of the Itamboatá River, considered an important source of water supply for the metropolitan region of Salvador. It is one of the main protection areas of the Recôncavo Norte Baiano, characterised by a hot humid climate and beautiful beaches beside dunes with vegetation native to sandbanks. There are also mangrove swamps rich in biodiversity in the estuary of the Joanes River, in addition to remaining areas of Atlantic Forest and associated avifauna. The area of the plant has 801,000 m² of environmental reserve and 53 m² of built area. The reserve was started in 2006, in a partnership with the Terra Mirim foundation and UFBA (Federal University of Bahia), with the carrying out of an inventory of water resources, fauna and flora around the units, and the drawing up of a plan for the opening up of hiking trails, together with an environmental project for youngsters in the community.
The plant of Atibaia, in Tégula, is also located in an environmental preservation area, with a total size of
4,881 m², on the banks of Ponte Alta Stream. This area consists approximately of 20% of native vegetation with the remaining area consisting of low growing vegetation and pasture.
At SAMA, approximately 80% of the 4,500 hectares of the area under protection is maintained as a forestry reserve, located in the Serra de Cana Brava, in Minaçu (GO). The mining company also maintains a Conservationist Plant Nursery, being a habitat that is protected and regulated by IBAMA. EN11 EN13 EN15
All Eternit's plants, as well as the mining company SAMA carry ISO 14,001 certification, which establishes standards for the control and mitigation of the Company's impact on biodiversity in the locations where they are installed. As part of the risk map required by this certification, more than 2000 points of attention have been drawn to with respect to the environment. Tégula is in the process of carrying out adjustments to apply for certification. EN12
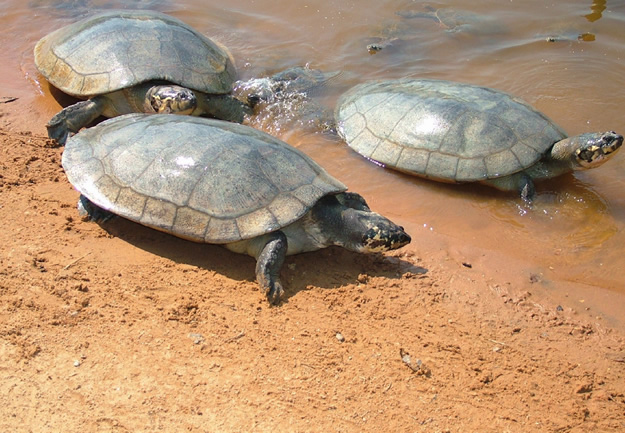
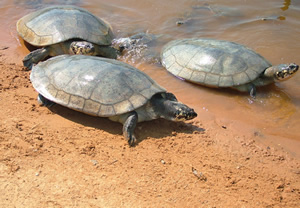
Chelonia Project - Amazon turtles
Protected or restored habitats | ||||||||
Location | Colombo (PR) Plant | Simões Filho (BA) Plant | SAMA Minaçu (GO) | Atibaia (SP) Plant - Tégula | ||||
Stage | Environmental Reserve | Environmental Reserve | Environmental Reserve | Environmental Preservation Area | ||||
Body responsible for study | SPVC – mapping of fauna and flora | Fundação Terra Mirim – mapping of fauna and flora | Ibama – Chelonia Project | Paulo C. R. Rocha (land surveyor) - assessment of permanent preservation area | ||||
Length of time of management of the area | Since 1975 | Since 1967 | Since 1999 | Since 1994 | ||||
Size m2 | 58,377 | 854,000 | 36,000,000 | 4,881 |
CONSERVATION
In 1995 SAMA set up the Chelonia Project, in partnership with the IBAMA (Brazilian Environmental Institute), for the conservation of native species of Chelonia, such as such as Amazon turtles, tracajás (side-necked) turtles, cágados turtles, tigres d’água (striped turtles) and jabuti tortoises. The objective is to raise the sensitivity and awareness of the community about the need to take care of the environment. Currently, 809 Chelonia are under the protection of the program, which includes two additional activities: the management of the reproduction of the Amazonian turtle and environmental education.
Established in an area of 3600 m², it is the only Chelonia Conservationist Breeding Area, within a company in Brazil, and is considered a reference for this type of initiative. In addition to Chelonia, the project receives others species of wild animals from environmental protection bodies (State Environmental Police, IBAMA/fauna) for treatment and reintegration into the environment, such as macaws, parrots and monkeys.
In Rio de Janeiro, Eternit signed a partnership with Riozoo, the Zoological Gardens of Rio de Janeiro, adopting a chimpanzee and an owl as part of the project to Adopt an Animal. Since 2004 the Goiânia Plant has supported the preservation campaign for the Araguaia River, which aims to provide environmental education for tourists and the population living along the bank of the Araguaia River.