02DIVERSIFICATION WITH QUALITY AND TRANSPARENCY
MANAGEMENT PRACTICES
In keeping with global trends, since 2007 Eternit has been a signatory of the UN Global Compact, whose principles refer to human rights, labour rights, the environment, and the combating of corruption, which guide the processes of the entire Group. In order to become part of the Global Compact, stakeholders were mapped out, together with their participation in the Company's activities in accordance with AA1000 methodology (click here), and identification which has contributed to improving Eternit's Management Excellence Program.
The Management Excellence Program, created in 2006 and improved in 2007, has the purpose of ensuring the integration of all the Company's management tools and the providing of guidance for manufacturing activities in a drive for continual improvement in the areas of health, safety and the environment. The program is implemented and monitored by the corporate area for Quality, Health, Safety and Environment, which consists of a multi-disciplined team.
Directives of the Management Excellence Program:
-
To assume a public commitment for the defence and protection of Human Rights, Children's Rights, Fundamental Rights at Work, preservation of the environment and the prevention of pollution, as well as the combating of corruption and the promotion of good corporate governance practices, by fulfilling all the requirements that apply to Eternit's activities.
-
To attribute worth to human capital, meeting international standards covering work practices, the prevention of accidents and occupational diseases, in the belief that the Company's employees are fundamental in achieving its goals.
-
To act in an ethical manner in relationships with society, shareholders, suppliers and customers, seeking to achieve sustainability in its businesses.
-
To adopt the best practices in the running of its industrial, commercial and administrative processes, always committed to continuous improvement and efficiency in its management system.
-
To ensure the safe use of chrysotile asbestos, exceeding the minimum legal standards and the other requirements demanded in its segment.
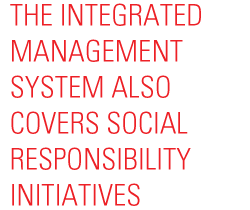
In addition, an Integrated Management System is used which, in addition to the areas covered by the Management Excellence Program, also covers actions on social responsibility and has the commitment to ensuring fulfilment of the legal requirements referring to the safe use of chrysotile ore. Furthermore, Eternit and its outsourced transport companies meet the requirements of PSQ Crisotila (quality program for the sector). Compliance with this program by Eternit is audited on a regular basis.
Continuous improvement is also monitored using the BSC (Balanced Scorecard) tool, which provides assistance in the creation of objectives for each manufacturing process, focusing on the Company's economic and corporate governance targets. BSC is today considered to be a reference for the entire sector. Another management system adopted by Eternit, not only for its manufacturing, but also its management processes, is the proposal by ABS Consultoria, which has the aim of improving the Company's efficiency, and consequently its profitability.
The mining company SAMA has an Integrated Management System, which covers Quality, the Environment, Security, Occupational Health and Social Responsibility, with a rigorous commitment to complying with the legal requirements that refer to the safe use of chrysotile ore.
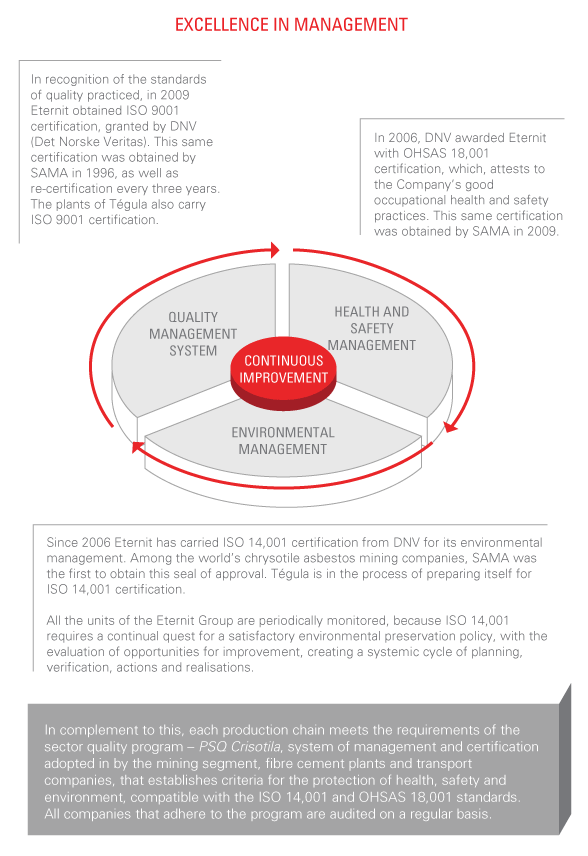
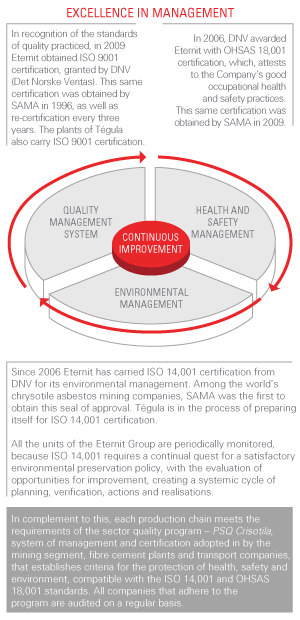