01A DIVERSIFIED COMPANY
FINISHED PRODUCTS
Eternit has an extensive portfolio of products for various stages of construction, being the market leader in the roofing, panel and cement slab segments. The Company has been diversifying its portfolio every year, always employing the same high-quality already recognised in its brand name.
Eternit's differentials
The Company's leadership position in the Brazilian fibre cement market is the result of a number of differentials achieved, as shown in the diagram below. On this list are intangible assets (click here), financial health, consumer confidence in Eternit's products and a good ability to meet market demand.
Fibre cement products offer attractive value for money, which serve all segments of the population. A technical study carried out by the IPT (Technological Research Institute) showed that fibre cement products using chrysotile asbestos make durable roofing that can last more than 70 years, without damage. Products made with synthetic fibres, on the other hand, last a maximum of 20 years.
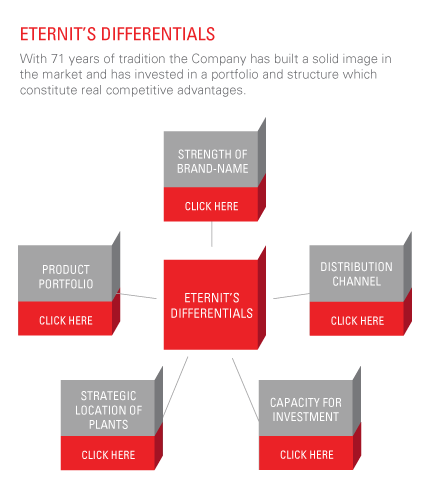

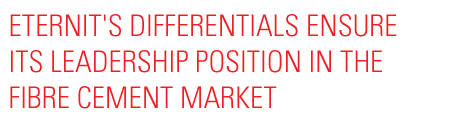
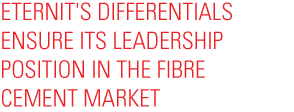
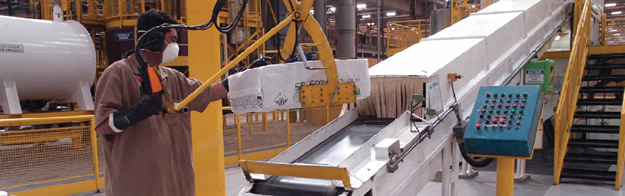
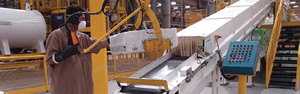
Supply of raw material - chrysotile ore sector
MANUFACTURER OF PRODUCT WITH CHRYSOTILE ORE
Eternit is the leader in the Brazilian fibre cement market, with a market share of 31%. Fibre cement is the result of a mixture of chrysotile ore with pulp, cement, lime and water. Each unit acquires its cement and lime from at least two different suppliers so as to avoid supply problems, and stores these products in automated silos, whose pressure systems send the stored material to the production area. The pulp, in turn, comes from recycled newspapers, acquired from co-operatives that collect old newspapers, and used cement bags collected from construction firms. The water is obtained from Artesian wells as well as rainwater, and is stored in tanks generally separated according to consumption purpose: use by staff or manufacturing.
Once the raw materials are mixed, the paste is captured by felt (manufacturing equipment), which forms a membrane, compacted with a cylindrical roller to achieve the desired thickness. Subsequently the paste is cut into standard patterns and corrugated to form the roofing panels. For the manufacture of the water tanks, moulds are used with different sizes. All products go through a curing stage, with the products being removed from the moulds after curing, for subsequent inspection and stocking.
It should be pointed out that all Eternit’s manufacturing processes are automated and enclosed, ensuring total safety for employees. Investment in technology in this area has resulted in Eternit becoming the only company in the world to have managed to automate the moulding of fibre cement roofing tiles with a design similar to that of ceramic tiles (Eterville – click here). In addition to this, all the Company's processes are sustainable, because everything is reused. The water used in the production is kept in a closed circuit, which avoids waste and run-off into the environment; while the offcuts from the paste membranes, as well as those tiles which fail to pass quality inspection, are reincorporated in the production process.
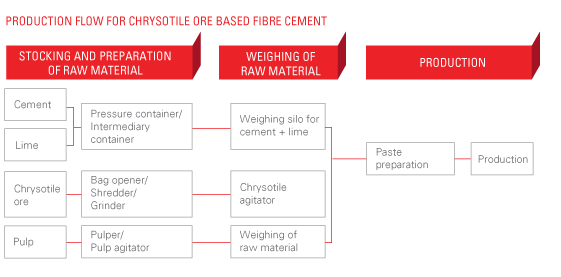
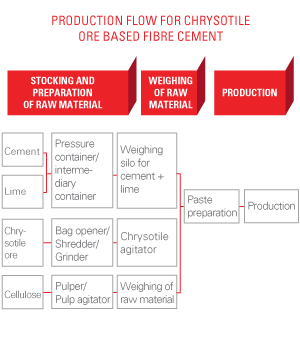
MANUFACTURE OF PRODUCTS WITHOUT CHRYSOTILE ORE BASE
Eternit has expertise in the manufacture of fibre cement products without the use of chrysotile ore. The Company has been manufacturing parts for roof construction systems and tiles with this technology, from 2000 and 2009 respectively, with a view to supplying markets where this fibre is restricted.
The Company's entire industrial park is prepared for this type of manufacturing process, which is similar to that used for chrysotile ore, with only the pulp of fining procedures being changed.
MANUFACTURER OF POLYETHYLENE-BASED PRODUCTS
Eternit produces polyethylene water tanks at its unit in Rio de Janeiro. The manufacturing process, which consists of the addition of polyethylene resins to moulds, cooling and finishing, results in a high quality product totally in agreement with the precepts of the ABNT (Brazilian Technical Standards Association).
MANUFACTURE OF OUTSOURCED PRODUCTS
The metallic tiles, vitreous chinaware, lavatory seats and water pipe filters that make up the Company's portfolio are not yet manufactured at its units. Production of these items is outsourced, but they are sold under the Eternit brand-name.
To guarantee the quality of the end-product, Eternit's quality team carries out on-site visits to inspect installations, production standards and employee safety aspects.
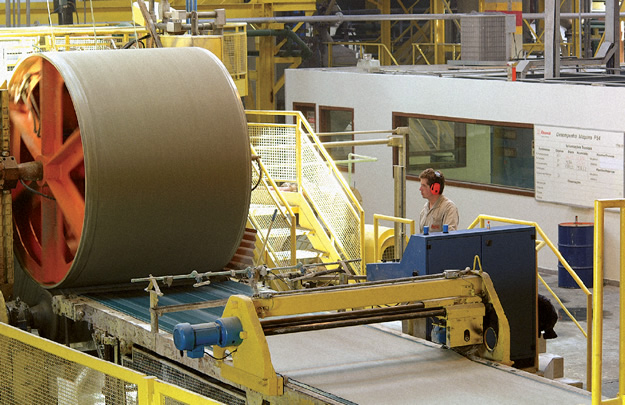
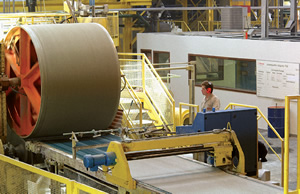
Fibre cement tile production machine
MANUFACTURER OF CONCRETE TILES
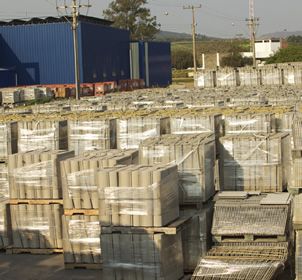
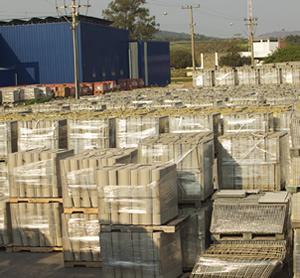
Stock of concrete tiles at the plant at Atibaia/SP
The concrete tile production process begins with the receipt of the raw materials. The cement is stocked in silos, while the sand is stored in bays. All the raw material is weighed. The sand is also sieved, and subsequently mixed with the cement, water and pigments, to form a paste.
The paste is mixed in a piece of equipment known as the mixer. The mixture produced is sent to a machine, which extrudes and separates the tiles. At the next stage, varnish is applied, with the tiles subsequently being sent to the curing chamber, where they remain for approximately 8 hours.
After the curing process, the tiles are palletized, and subsequently transported to the stockyard, where they remain stored until being released by the Quality Control Sector for sale.
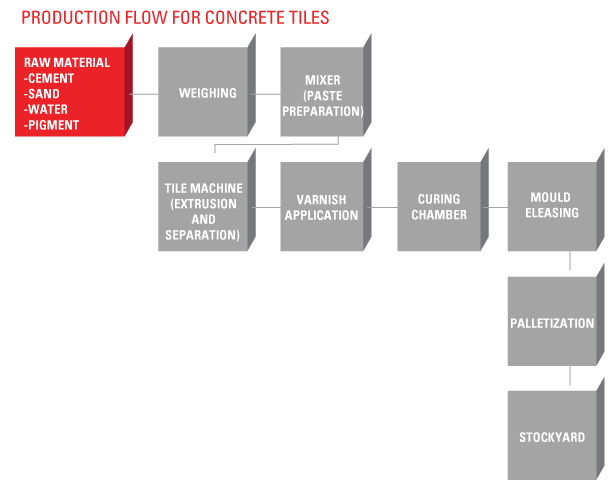
