01A DIVERSIFIED COMPANY
MINING
SAMA S.A. – Minerações Associadas is the only chrysotile ore mining company in Latin America and the third largest in the world in operation. Having a global market share of 14%, the company is positioned only behind Russia, with 48%, and China, with 22%.
The mining company ended 2010 operating at full capacity and has an installed production capacity of 300,000 tons a year. SAMA has a plan to increase current capacity to 350,000 tons, but is waiting for a ruling on the part of the Supreme Court on the question of the mining of chrysotile asbestos in Brazil (click here). Extraction from the mine began in 1967, and taking the current level of production, the mineral deposit has a useful life of a further 31 years, seeing that chrysotile ore is not a renewable resource. This calculation, however, may vary in accordance with any expansion in production.
The annual amount of rock handled, which includes the ore and sterile tailings, comes to 5 and 11 million tons, respectively. The chrysotile fibre represents 7.2% of the crushed mineral. Most of the sterile tailings are deposited in piles, which are subsequently covered with soil and re-covered with vegetation. A small part of the sterile tailings is used for arts and crafts production as part of the Sambaíba Program (click here).
SAMA is located in the municipality of Minaçu, in the North of the state of Goiás, 510 kilometres from Goiânia. Installed on the left bank of the Tocantins River, it occupies a state concession area covering 4500 hectares, of which less than 20% is used for mining. Of the remainder, reforestation areas account for 10%, while a nature reserve of native vegetation accounts for 70%.
At the end of 2010, SAMA had 588 direct employees, of which 180 reside in the housing-estate belonging to the mine. SAMA is one of the largest payers of ICMS taxed to the state of Goiás, stimulating economic movement in the region and the state.
DIFFERENTIALS OF THE MINING COMPANY
SAMA is different from its global competitors because of its good practices with regard to the environment, health and safety, and its reputation for maintaining a stable quality of the fibre it produces. This subsidiary of Eternit was the first chrysotile ore mining company in the world to obtain ISO 14,001 and OHSAS 18,001, certification.
Another differential that the company has is the guarantee that it offers for the delivery of chrysotile ore on a given date. With regard to its socio-environmental practices, SAMA is a signatory of the UN Global Compact, as well as being a supporter of the UN Millennium Targets. In 2010, it was the only Brazilian mining company invited to participate at the Leaders Summit, a United Nations event held in New York to debate themes related to the transformation being implemented by sustainability in various markets, based on the principal economic and environmental events over the last few years. Over a period of three days, company CEOs and representatives of government and society discussed ways of developing and applying a global strategy for companies and other institutions in society to integrate environmental, social and corporate governance aspects into their businesses. Participation at this event was of extreme importance because it permitted SAMA to present its views at the debate, having positive repercussions on the mining company's image.
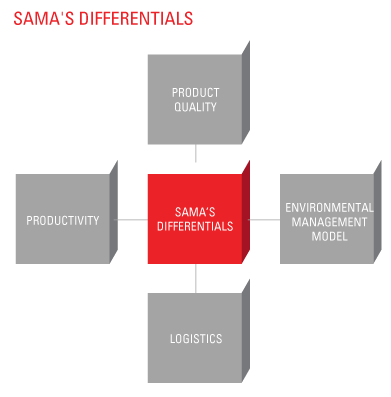
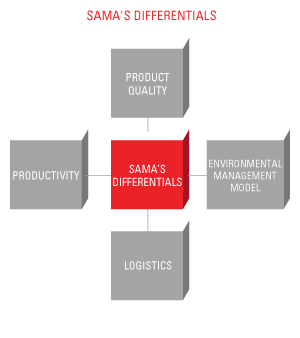
EXTRACTION AND PROCESSING OF CHRYSOTILE ORE FIBRE
The process of extracting chrysotile ore is initiated after the receipt of the sales plan. Based on this, a production and mining plan is drawn up, which defines the locations where the inroads are to be made in the mine. At the rock faces drilling is carried out with the rock being broken up through the detonation of explosives. This procedure is covered by a series of measures to ensure safety. The explosive, is in truth, an emulsion based on ammonium nitrate prepared in the location where the explosion is to be carried out and is only made sensitive when accessories are put in place (boosters and detonators) after being inserted in the hole where it is to be detonated. Subsequently, the processing stage begins with the transport of the ore resulting from the detonation to the primary crushing area (mine entrance), with the sterile rock being sent to the tailing piles, where it is later planted with native vegetation.
The entire extraction process, from the trackway to loading on the trucks, is carried out under constant dampening to avoid particle emissions. From the silos to the processing area the ore is transported on enclosed conveyor belts. The fibre then goes through further processes in which any further sterile rock is removed, and classified into long, medium and short fibre lengths. The end-product is bagged in 50 kg blocks and stacked on pallets in amounts of up to two tons, which are subsequently covered by a removable plastic film.
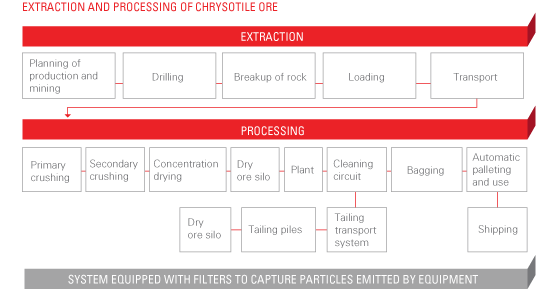
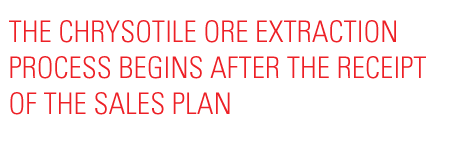
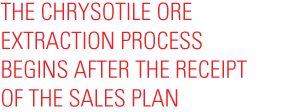